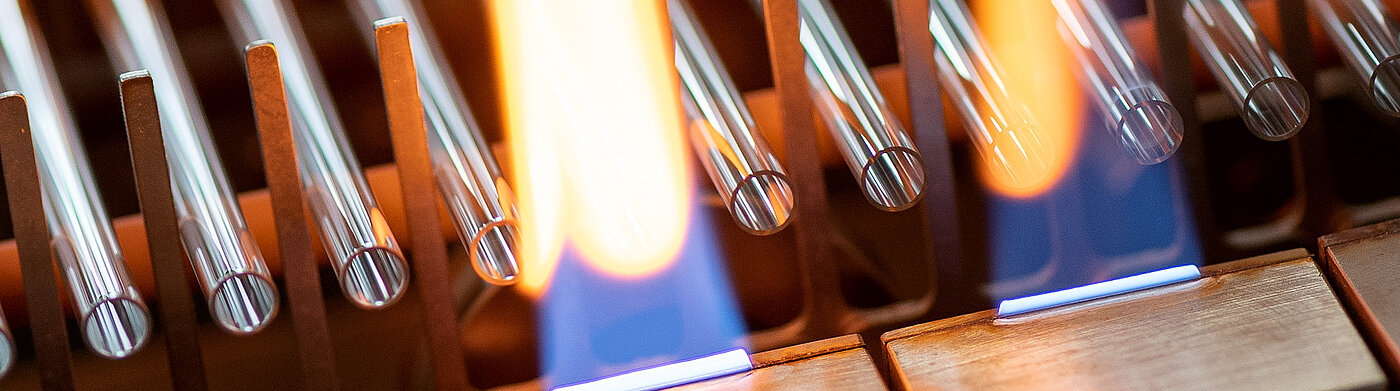
End machining
From glass tube blanks to sample tubes with flat bottoms and beaded rims, drawing pipettes or a tube with a kink: all these product features are achieved through the processing and forming of our various raw materials.
Hot forming with forming tools
When hot forming with tools, the glass is heated until it reaches a soft, doughy consistency. Forming tools are then used to create a profile, for example at the end of a tube. Here, the tube is supported from the inside, while pressed into a form from the outside with the forming tool.
Various symmetrical or asymmetrical forms can be rolled on to the glass, such as collars (like the beaded rim), or even threads and flutings.
Bottom forming
There are a number of different bottoms possible: round, flat and conical bottoms, special bottoms and pedestals. Hot forming is used to shape the various designs. The glass is not initially rolled, however, but heated approximately 20 mm from the end and then drawn off from the main body. A flat bottom is created, which can be blown out with air to form a round bottom. Once the bottom is closed, it can be processed further and formed. Forming tools are used again here, for example to create a long or conical shape.
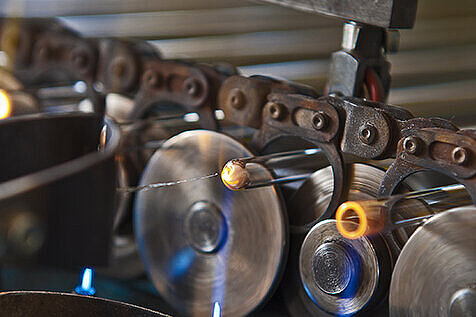
Notching, recessing & rolling
Special tools are used to form the glass in a certain position, such as a spout for measuring cylinders, or for notching a piece of glass from the wall (punching). Holes can also be made in this way. In addition to machining the edges, changes can also be made to the length of the glass tube before it is formed. For example, grooves or tapers can be rolled into the tube.
Forming of tips and outlets
Hot forming with forming tools is used to form tips with a defined outlet on larger glass tubes, as seen on graduated pipettes, for example. An internal tool is also used here to calibrate the inner channel to a certain length, while at the same time the glass is formed from the outside into a round shape on a mandrel. It is also possible to form straight outlets along short lengths of glass.
Drawing and forming of tips and microtips, nozzles
The tips of pipettes are created using a hot forming process. By heating and then drawing them out, tips of all shapes and sizes can be formed. For micropipettes, tip diameters < 1 µm are even possible.
Fire polishing & melting of cut edges
Fire polishing is the process used to round off ground cut edges or sharp broken edges. The cut edges are briefly subjected to an intense heat in order to melt their surface. Depending on the heat and duration of the flame, results can vary from slight to extreme rounding, or the merging of the ends which in turn involves sealing and shaping of the bottom. Fire polishing can also be used to make frosted polished edges transparent again. Or even polished surfaces on glass parts.
Laser polishing of cut edges and surfaces
Laser polishing produces results similar to those of fire polishing. However, instead of using a fairly large diffuse flame, a slightly intersected laser beam delicately and precisely heats the surface of the glass parts. This process can be used on the smallest of structures, such as ground nozzles tips or micropipettes.
Mechanical grinding of facets and beveled edges
Cut or broken edges on glass are quite sensitive. If they come into contact with harder materials or are subjected to pressure, they can quickly splinter. However, soft materials such as rubber, for example sealing rubber, can also be protected against damage by the glass cutting edge. Facets, chamfers and beveled edges are predominantly ground, with hot forming also an option here.
Mechanical/optical polishing of cut edges/front surfaces
For many applications, edges that are simply cut or ground/sawn will suffice. However, when optics play an important role, the evenness and transparency of the surface finish may need to be considerably better. Here, the ends of tubes and rods or other components can be mechanically polished until the preferred optical quality has been reached.