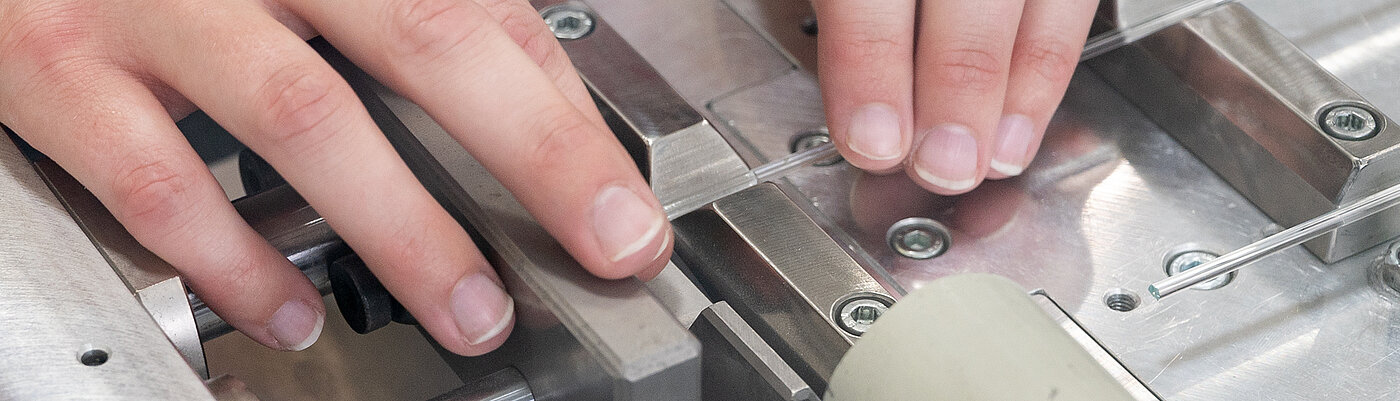
Cutting
Various techniques are required when it comes to cutting anything from the finest capillaries to the most solid rods. Whether by hand or with a machine, using a laser or a blade: the application must be appropriate to requirements. Because the cutting edges are just as different as the method used to create them.
Score cutting and breaking
Score cutting is actually quite simple: the surface of the glass is slightly damaged, with a groove cut into the glass in a process known as scoring. This serves as the breaking point. Subjected to bending stress and possibly a slight pull, the glass will then break.
360° circular score cutting
Circular score cutting is the procedure used to create particularly flat cutting edges on tubes and capillaries, without the need for grinding. The score required to break the glass is made to the glass surface with a circular motion. The resulting notch ensures a clean break and prevents any chipping or protrusions on the cut surface. The 360° rotation also leaves a cutting edge that is very slightly beveled.
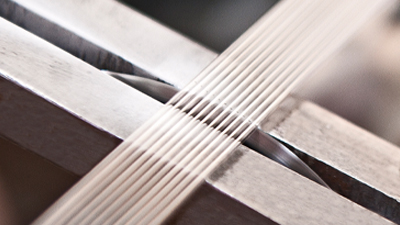
Manual 360° score cutting
Laser cutting including laser thermal shock cracking
Laser sublimation cutting involves vaporizing the glass with a laser. Air is constantly circulated around the tubes, largely preventing condensation from forming on the glass. To separate the parts, a targeted stream of air is applied to the cutting slit in order to further support the break.
Just like the conventional thermal shock cracking procedure, there is also a localized heating of the component, before it cracks due to the rapid cooling and resulting “thermal shock”. The use of a laser for thermal cracking can be advantageous for some types of glass, as the application of heat is more targeted than when using the more traditional oxyhydrogen flame.
Thermal cracking
With thermal cracking, the glass is exposed to localized heating, before it cracks as a result of the rapid cooling and resulting “thermal shock”. Depending on the type of glass, an initial crack may need to be introduced, which facilitates the development of the thermal shock.
Abrasive cutting & Sawing (individually or in bulk)
For the abrasive cutting and sawing of glass, a diamond-tipped circular saw is passed through the glass. This procedure therefore makes it possible to achieve very flat cuts and maintain tight length tolerances. Abrasive cutting is particularly suitable for thick-walled tubes and capillaries, or extremely small and short sections. The cut surfaces of the parts generally have a frosted finish and may display slight chipping at the edges. Depending on the circular saw used, various cut surfaces can be created during the cutting procedure.