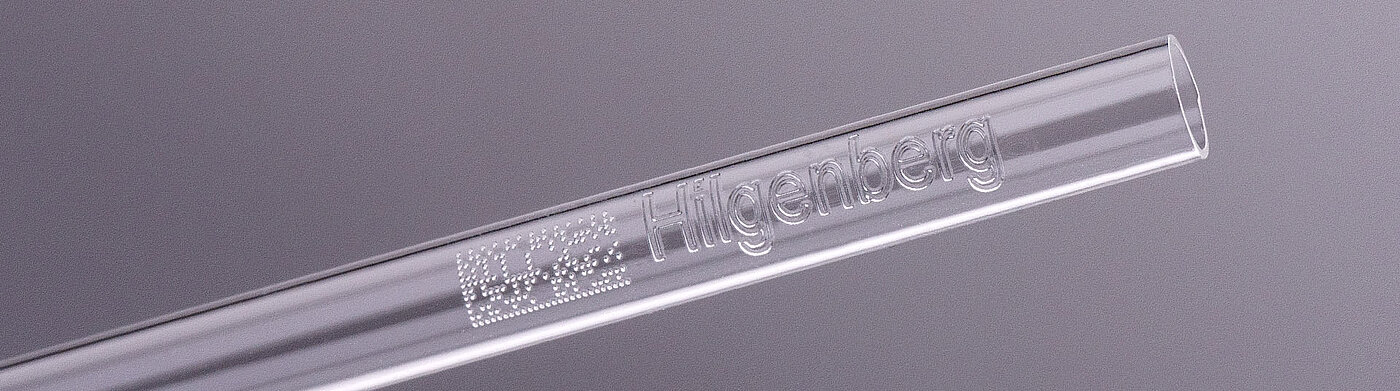
Surface processing
There are a number of ways to process the surface of a product: from the structuring of the surfaces to marking or frosting, it all depends on why you need it and what it will be used for.
Cylindrical grinding and mechanical polishing of the lateral surface
Many technical applications for glass must demonstrate a high degree of precision when it comes to external geometry, for example to ensure the perfect fit of tubes or rollers in bearings etc. Tubes and rods can be cylindrically ground for this purpose, with two approaches possible here. The tube parts can be placed between centering points. This allows for the parts to be ground concentrically to the center axis / internal diameter. Centerless cylindrical grinding of rods and tubes is also possible. This process does not affect concentricity, and there is an accurate cylindrical grinding of the lateral surface only.
There is also the option of polishing the parts again after grinding, returning the surface that was finely frosted from grinding to a transparent state.
Structuring of surfaces
Glass surfaces can be structured using a laser. There are generally two ways to approach this: thermal structuring, which involves melting a specific area of the glass and causes a raised structure to form on the surface of the glass, or cold structuring, whereby a very localized thermal shock breaks off material from the surface. A type of frosting results, which is very similar to the effects of sand blasting.
Marking and scaling of surfaces
Glass surfaces can be marked using screen, pad, or digital printing processes. There are various machines and service providers available for this. Internal printing capacities will be expanded in the medium term and complemented by an efficient digital printing process.
A CO2 laser is used to mark the surfaces of borosilicate glass and quartz glass.
Laser micro structuring and processing
Laser structuring involves using a laser to melt selected points on the surface or to vaporize parts of the surface material. There are few restrictions to the type of structure that can be created, and it also possible to use this process for marking or to create holes. It is particularly suited to quartz, borosilicate, and aluminum silicate glass.